Apparatus construction by Kremsmueller
Pairing innovative technology with decades of experience, we are in a position to offer you first-class solutions that are precisely tailored to your needs.
Product overview in apparatus construction
Our product range spans across a variety of specialized apparatuses and tanks designed for various industrial applications. Each product embodies superior quality and precise workmanship.
Additional services in apparatus construction
The components manufactured in Kremsmueller apparatus construction’s division form the heart of process engineering systems in all industrial sectors. We assist you every step of the way – from initial planning to the last screw – and remain at your side by providing maintenance, repair, extensions, and replacement construction.
Conversions & repairs
We offer comprehensive conversions and repairs of apparatuses and tanks to maximize the efficiency and service life of your plants.
Pickling shop
Our pickling shop applies the optimal surface treatment to your apparatuses and components to furnish them with flawless corrosion resistance and cleanliness.
Contract manufacturing
Take advantage of our extensive pool of machinery and our know-how to satisfy your specific production needs and benefit from the highest precision and quality.
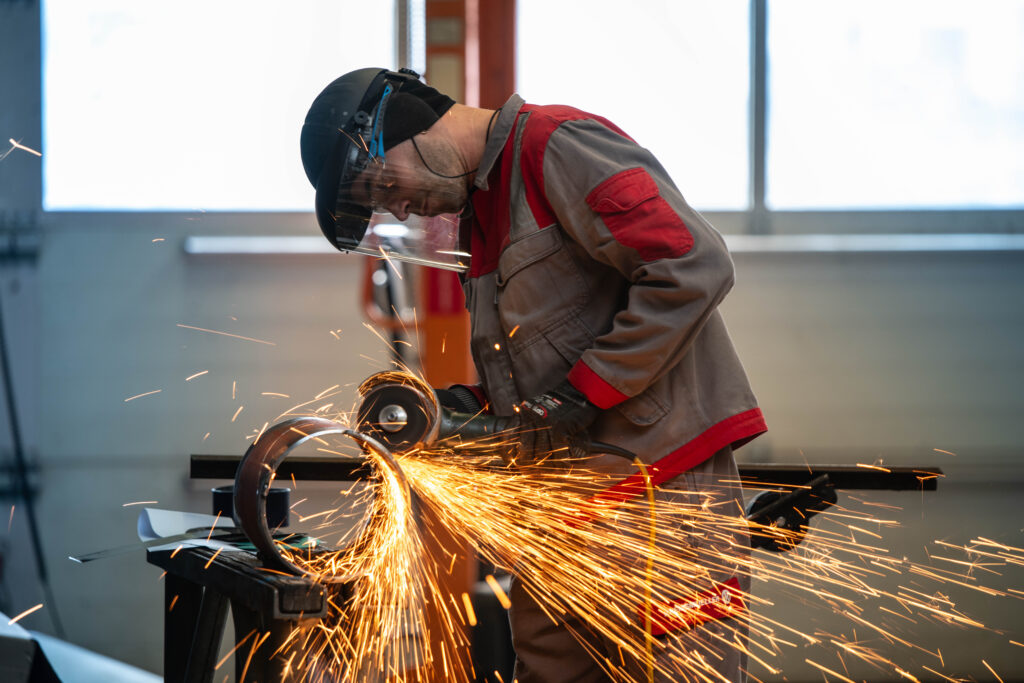
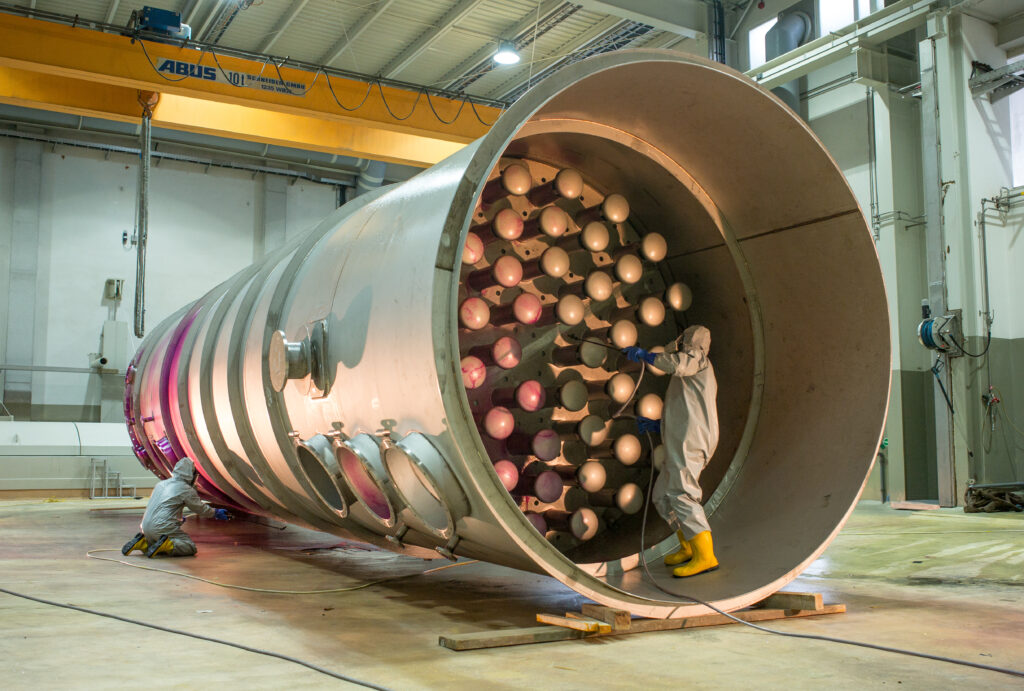
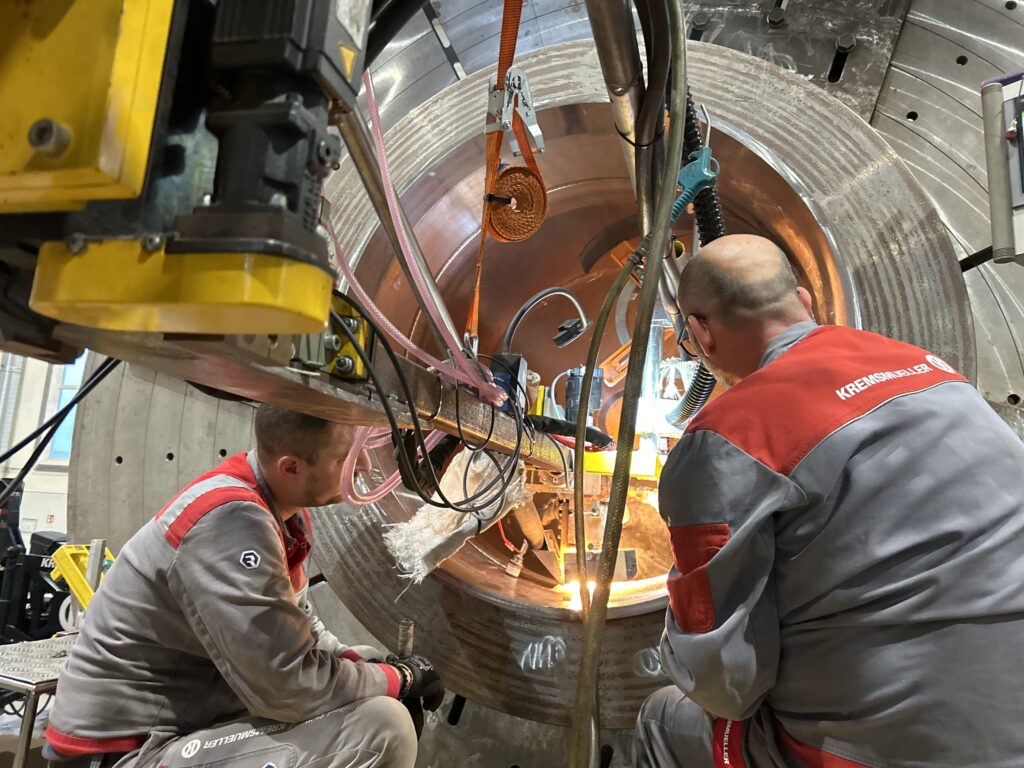
Our passion
We are the experts to consult when it comes to heavy and thick-walled apparatuses or the use of high-quality special materials such as stainless steels, titanium, and nickel-based materials. We love challenges and complex projects that require a great amount of know-how. We are also happy to take care of the assembly for you. What is more, we can contribute our comprehensive knowledge in pipeline engineering as well as in measurement and control technology, offering you a comprehensive solution.
Engineering
Demanding projects with a high proportion of engineering services
Teamwork
Joint efforts from our colleagues in pipeline construction and measurement and control technology
Speed
In cases of urgent need, we will work for you in 3 shifts
Thick-walled
Heavy and thick-walled apparatus for high pressure conditions
Special materials
High-quality special materials such as stainless steels, titanium, and nickel-based materials
Assembly
Delivery including installation and assembly
Columns
We offer custom column solutions that are tailored to fit your specific process requirements perfectly. Our columns can either be delivered in one piece up to a length of 62 meters or assembled on site in two half-sections by means of a “Golden Weld”.
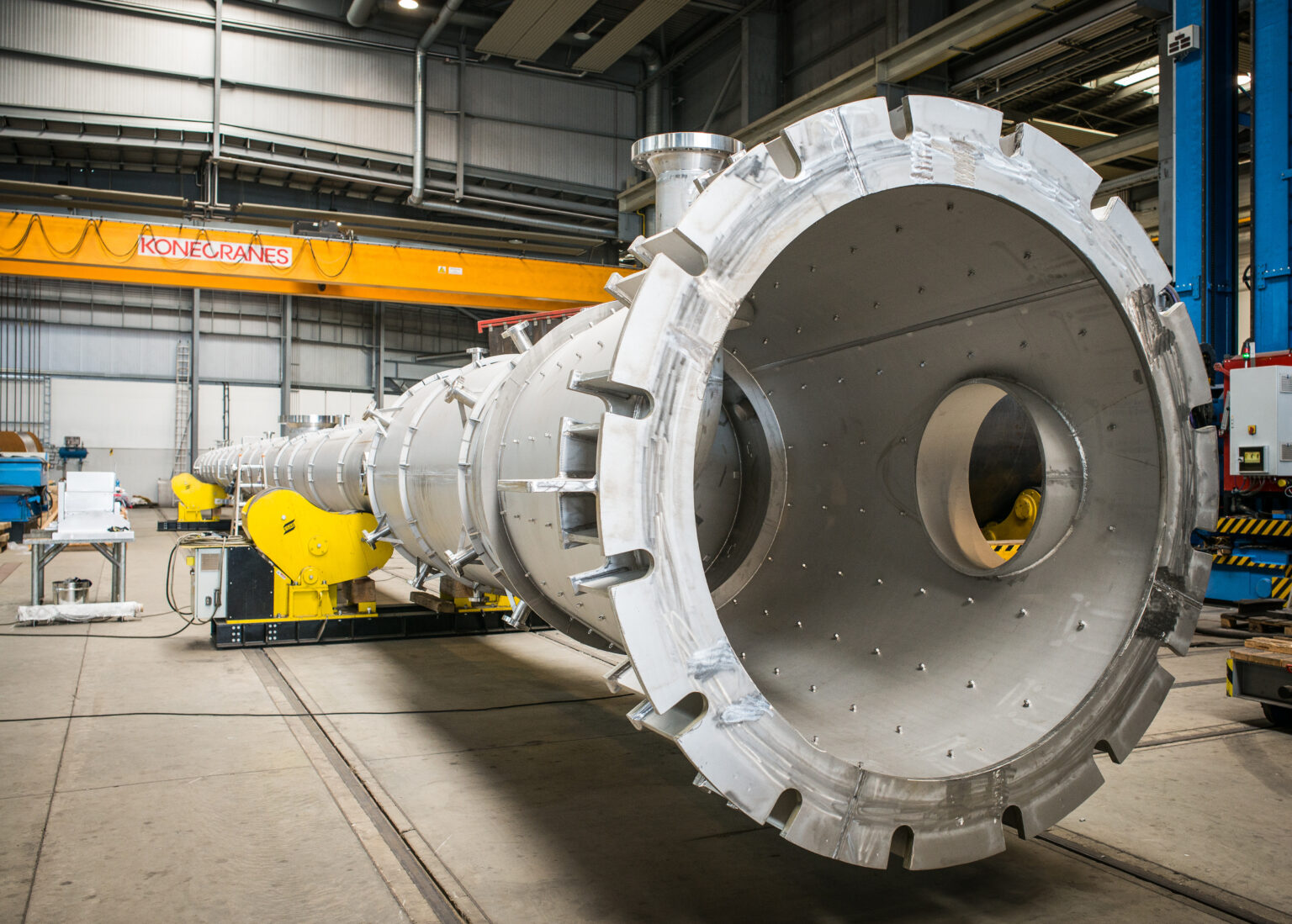
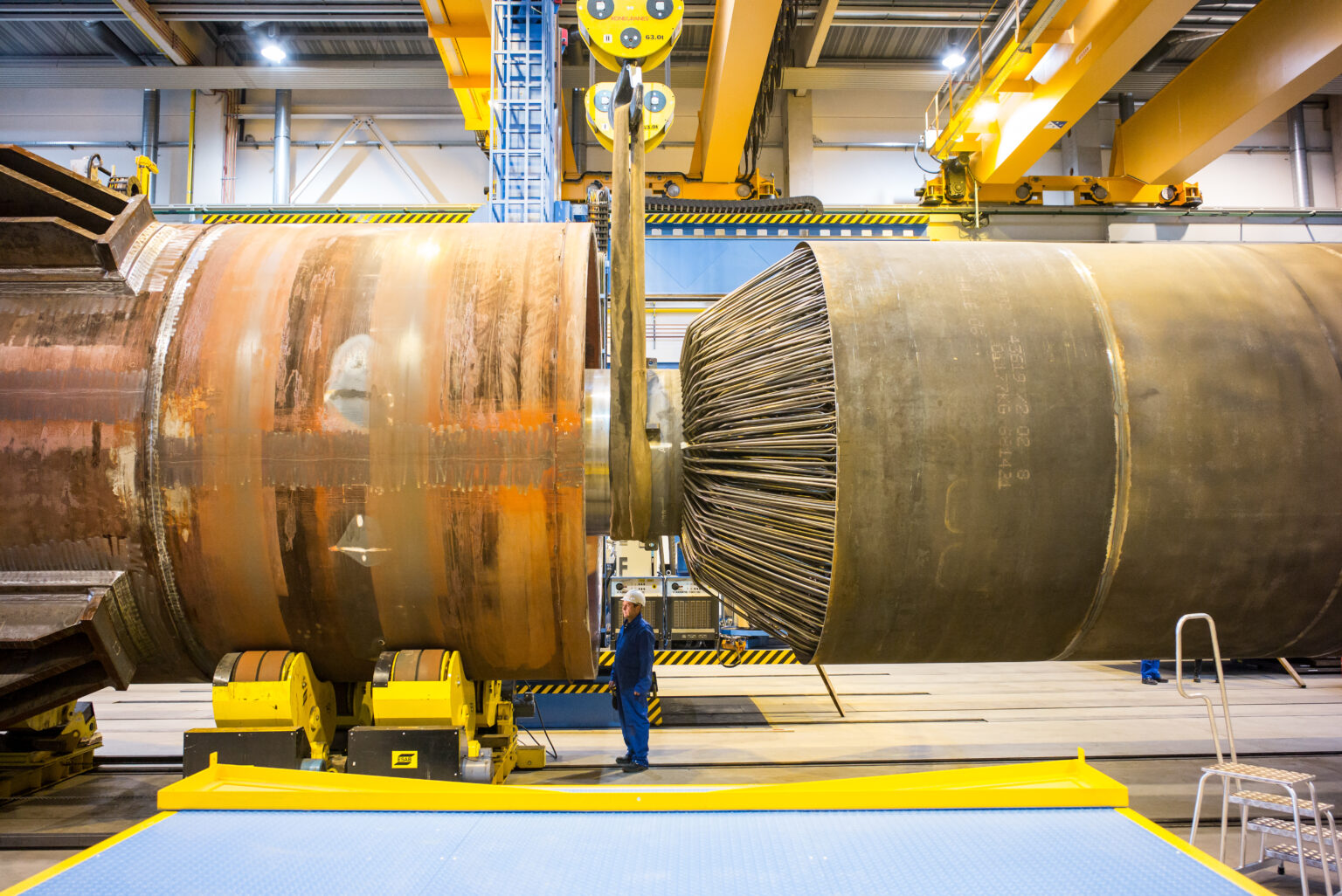
Reactors
Our expertise in sheet metal processing allows us to roll sheets and process materials up to a thickness of 160 mm and 300 mm, respectively. For applications involving corrosive media and high pressures, we rely on roll-clad or explosive-clad sheets. We plate transitions and flanges with great efficiency and precision using electroslag welding to ensure the maximum quality and reliability.
Thin-film evaporators
At our state-of-the-art technical centre, we develop tailor-made thin-film evaporators and dryers that will optimize your process. Whether you require initial extraction or recovery of valuable products or the efficient processing of residual materials – we offer you the solution that suits your needs best.
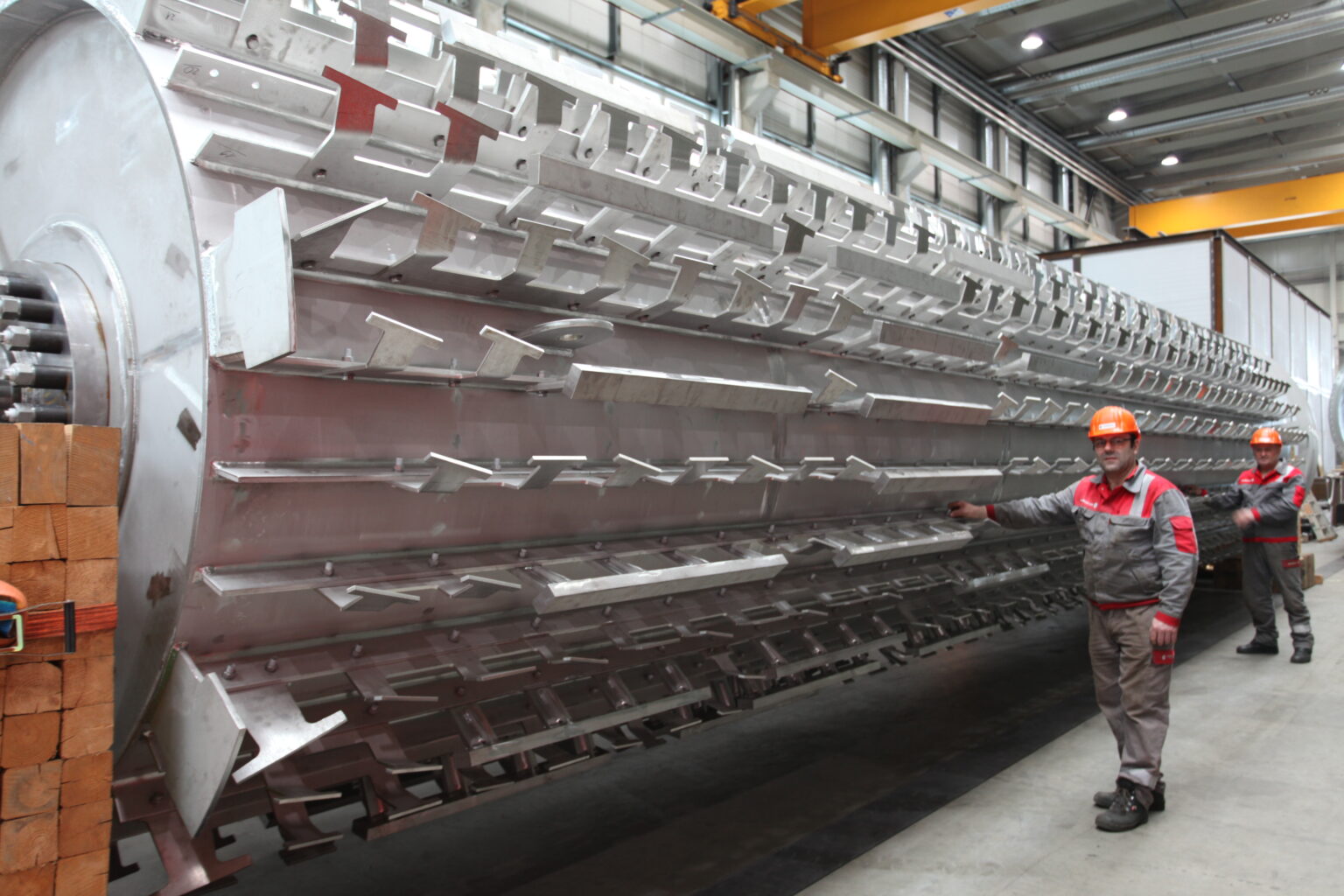
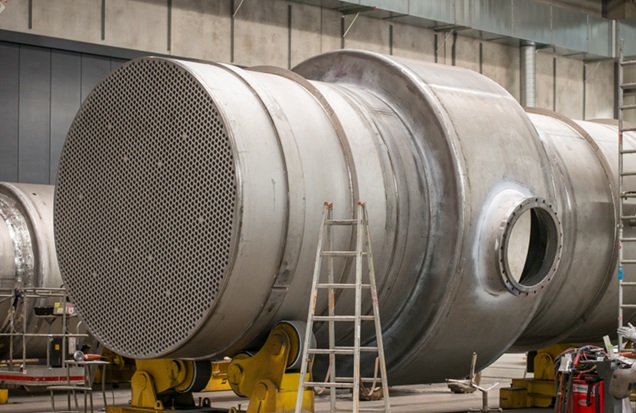
Heat exchangers
We manufacture heat exchangers with a tube sheet spacing of up to 20 meters and a weight of up to 250 tons. Smaller heat exchangers made of high-quality materials or for high pressure requirements are part of our portfolio as well. Rely on our expertise in the production of efficient and reliable heat exchange systems that are perfectly tailored to your specific requirements.
Tank construction
Our expertise in tank construction enables us to develop on-site storage tanks that meet the highest quality standards and fit your individual needs to a T. It will be our pleasure to advise you on the optimal use of space and the reduction of your costs by considering different diameters and heights for your required storage volume. For environmentally hazardous substances, we additionally equip our tanks with collection trays and monitored raised floors to prevent the medium from escaping into the environment.
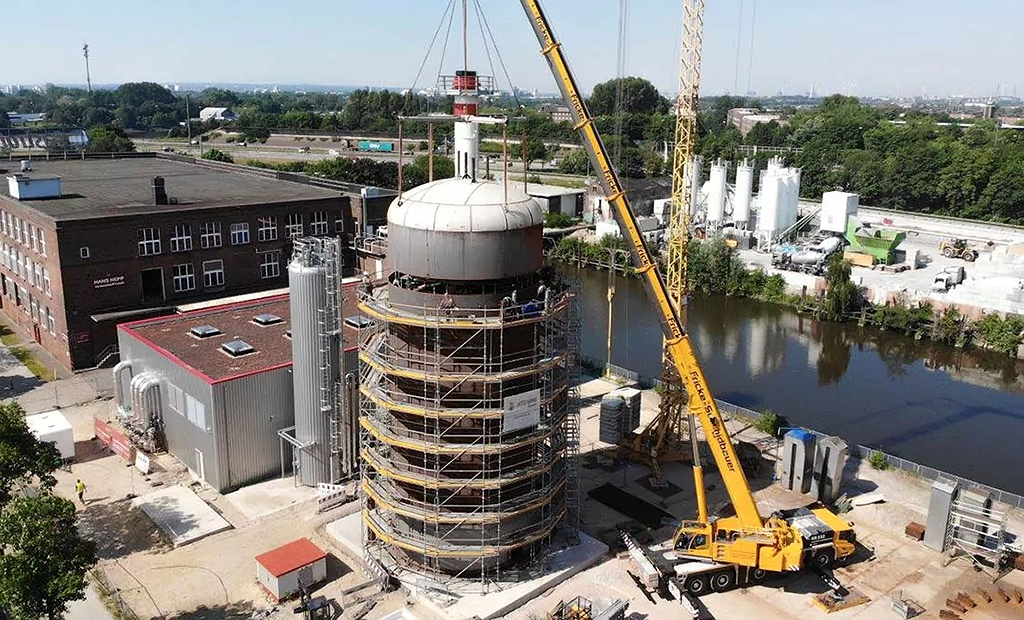
Heat storage tanks
Our heat storage solutions are designed to maximize the energy efficiency of your systems by storing excess heat and releasing it when needed. Their high capacity and reliability allow them to make a substantial contribution to the optimization of your energy processes.
Skid systems
Our skid systems are a reflection of our ability to blend our apparatus construction, pipeline construction and measurement and control technology skills into one all-inclusive solution – from planning to on-site commissioning. Conducting test runs (FAT) at our factory, we ensure the high quality you need for your process.
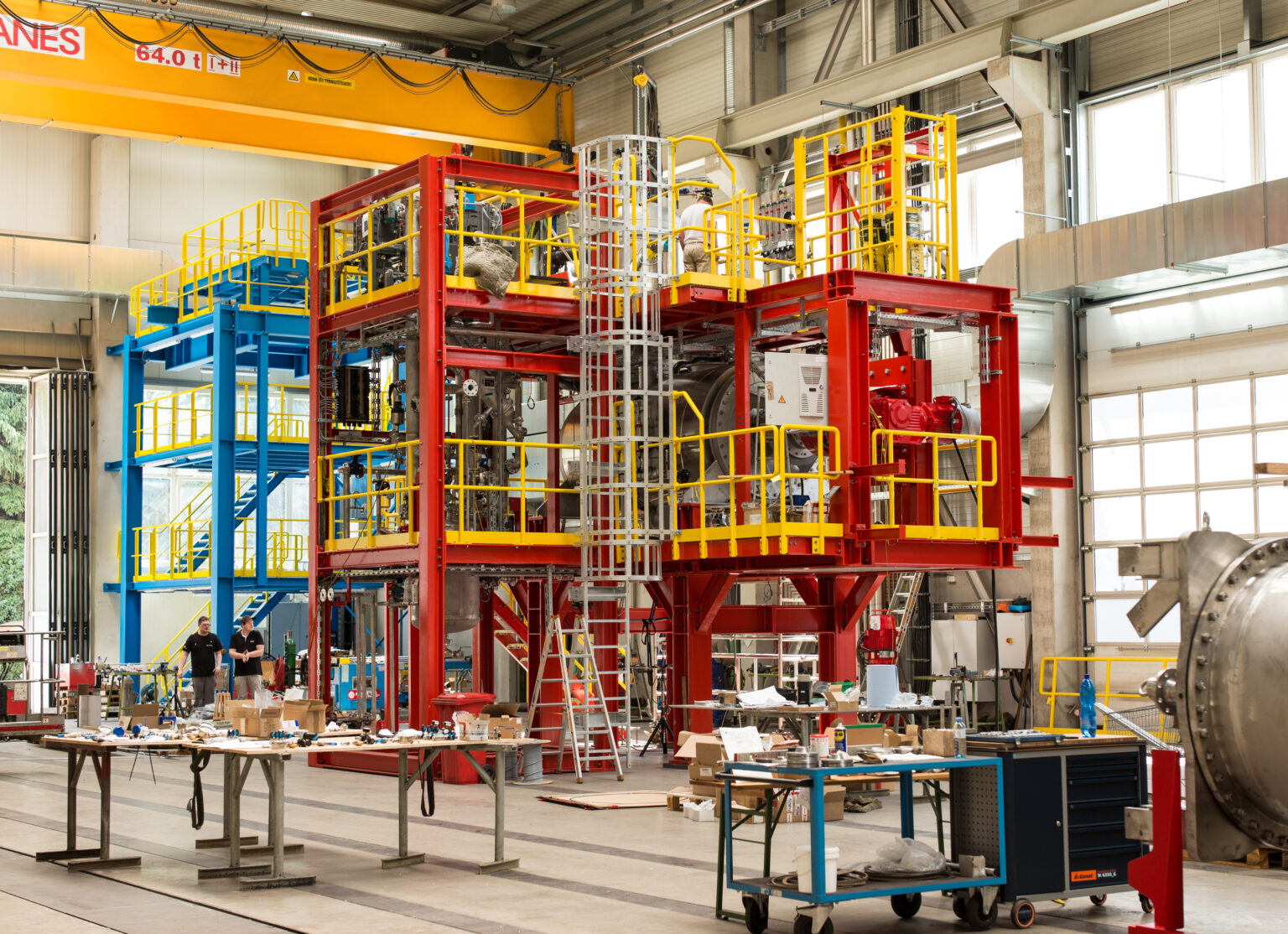
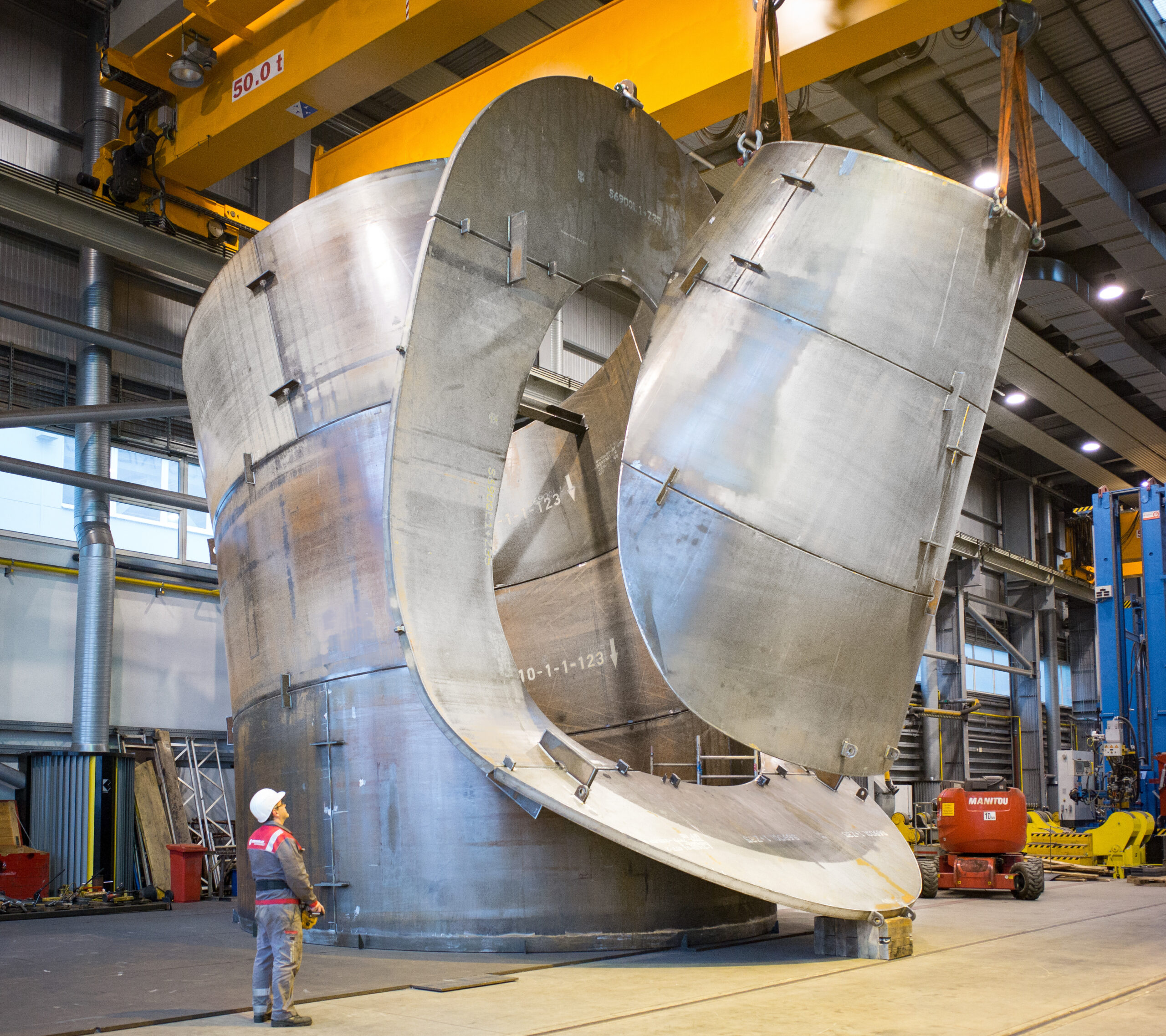
Steel hydraulic engineering
We offer a comprehensive range of services in steel hydraulic engineering – from planning and construction to production and assembly in the shaft. Our expertise also extends to the manufacture and worldwide supply of special parts such as thick-walled Y-pipes. Place your trust in our experience and proficiency in crafting tailor-made solutions in the field of steel hydraulic engineering.
Ask our experts!
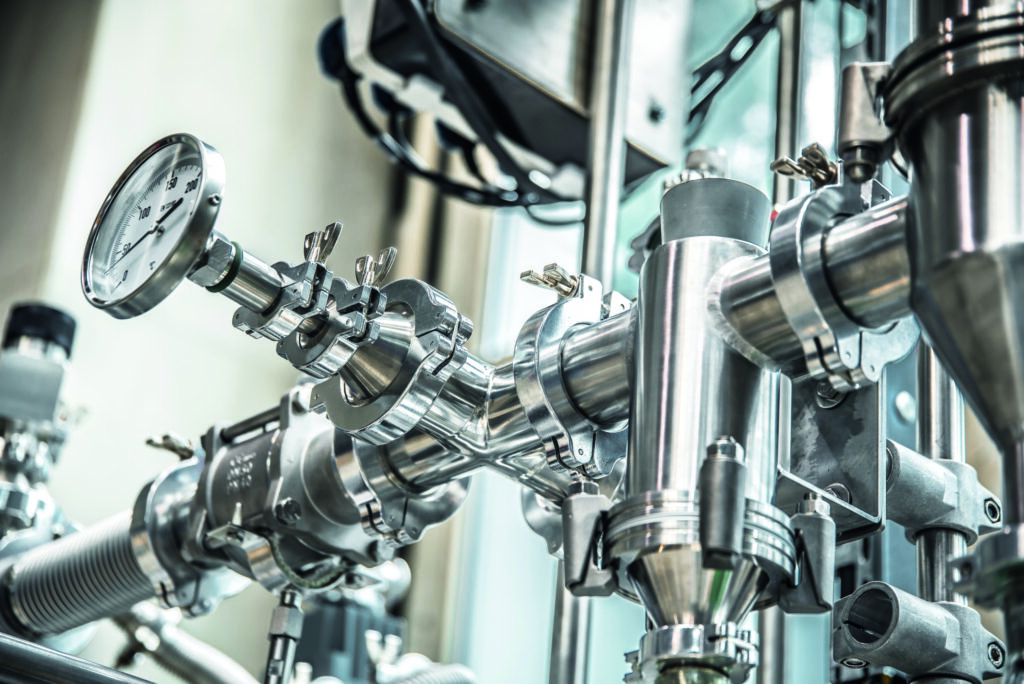
Kremsmüller Apparatus Engineering
Kremsmüller Test Center
Focusing on energy efficiency and environmental friendliness, the Kremsmüller Test Center provides a top-tier platform for the development of sustainable solutions in various industries.
We go above and beyond the services rendered by conventional research institutions. Our expertise in apparatus construction lets us factor in your future overall system as soon as we receive your initial request.
Not only do we offer you key figures, consumption numbers and information on the theoretical feasibility, but we also analyse the economic aspects and the actual feasibility of your undertakings. The assistance we lend you will not only let you realise your project, but will also turn it into an economic success.
On the move in other dimensions
Production at the headquarters near Wels:
Diameter up to 4.8 meters, length 50 to 55 meters, weight up to 250 tons (road transport)
(transport by road)
Assembling hall Linz/Donau
Diameter up to 10 meters, length up to 80 meters, weight up to 500 tons (transport by barge)
Certificates from Kremsmueller
Our extensive range of certificates and approvals underline our commitment to the highest quality standards and safety. We are proud to hold numerous international certifications, including international approvals such as ASME and Chinastamp. These approvals confirm our expertise and reliability in the manufacture of high-quality equipment and systems that meet the strict requirements and standards worldwide
Customised apparatus engineering for all requirements
Apparatuses are custom-made products:
Precisely designed to meet the requirements of our customers. Which materials are used depends on the processes, the media and the required process parameters of the respective apparatus.
Important to know:
Kremsmüller Apparatebau processes a wide variety of steels and other materials. This means absolute flexibility for our customers.
C-steels from cold toughness to high strength
SA516-70, 16Mo3, 13CrMo4-5, SA335-P92, S690QL,..
Corrosion-resistant stainless steels
SA240-304, SA240- 316Ti, 1.4462, 1.4539, 1.4845, 1.4841,…
Roll clad and blast clad steel, weld cladding
P355NL2+1.4462, A516 Gr.70+ AISI 316L, P420NH+1.4541,…
Special materials (nickel, titanium, aluminum, copper)
Allo59, Alloy 400, Inconel 600, Ti gr2, Ti gr12, CuNi 90/10, T3003, T5049, T6082
Tight schedule? Ask us for the fastest way!
We put your most important apparatus engineering projects in the fast lane! If your apparatus has to reach its destination on time, even with a short lead time, the Kremsmueller team picks up the pace – solution-orientated and cooperative.
Service and maintenance
Apparatus and systems must always run flawlessly and always be technically up to date. At Kremsmueller, apparatus engineering therefore also includes the following on request:
Regular maintenance to avoid expensive downtime due to repairs
Forward-looking maintenance planning in order to complete necessary work on the equipment as quickly as possible
Fast support for repairs
Expert advice on extensions and modernisations with the removal and installation of equipment in existing systems