Working under the hottest conditions
The I&C team laid 10 kilometres of cable for the automation and control of a steel casting system.
Two systems were installed for the electrical engineering of a ladle upender and a ladle fire. The I&C team was responsible for five MCC cabinets as well as for six control cabinets and operating stations each. To bring the systems to life, one kilometre of a ring conductor and about 10 kilometres of power and control cable were laid right across the works.
In an environment in which liquid steel is processed, such work is particularly challenging. The ladle fire heats up the steel casting ladles to up to 1100 degrees and keeps them hot. The required heating curves are controlled by the automation engineering. After the steel has been poured out, the steel casting ladle has to be prepared for the next batch. This is done in a ladle upender, which rotates the container, weighing about 64 tonnes, through 360 degrees for cleaning.
Would you like to know more about this project? Then click on the right on Contact (envelope icon) and you will be connected directly to our experts.
In an environment in which liquid steel is processed, such work is particularly challenging. The ladle fire heats up the steel casting ladles to up to 1100 degrees and keeps them hot. The required heating curves are controlled by the automation engineering. After the steel has been poured out, the steel casting ladle has to be prepared for the next batch. This is done in a ladle upender, which rotates the container, weighing about 64 tonnes, through 360 degrees for cleaning.
Would you like to know more about this project? Then click on the right on Contact (envelope icon) and you will be connected directly to our experts.
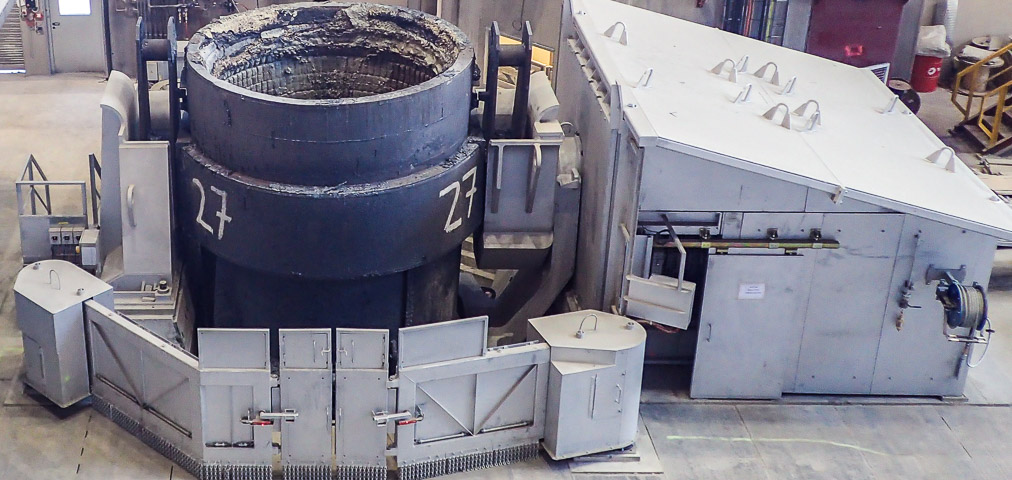