Glassy-smooth plant construction
New standards with regard to precision for the plastics industry.
The capacity of a leading plastics manufacturer was to be increased by a third. The existing gas phase reactors were to be the models, but the Kremsmueller experts made the design state-of-the-art. The innovative material Lean-Duplex is now being used. This means the maximum corrosion protection and perfect strength.
High-quality plastic is manufactured in the reactor. It is a decisive factor for the product quality that the tank must be free of traces of machining on the inside. Grinding and electro-polishing resulted in a glassy smooth surface with impressive precision. The requirements for optimum gas distribution were just as stringent. The production gas now reaches the reaction chamber through no less than 1228 guiding pipes.
The finished tank is 21 metres long, weighs 72.5 tonnes and has a diameter of 4.6 metres at its broadest point. The gigantic reactor was installed together with 180 tonnes of equipment, 170 tonnes of steel structure and 190 tonnes of piping. The entire I&C systems were also installed by the electrical engineering experts from Kremsmueller – using 86 kilometres of energy and instrument cables. Needless to say, the safety measures in the areas with explosive atmospheres were extremely stringent. The assembly work was so painstakingly planned in 3D that running operations were hardly disturbed: 90 percent of the work was carried out with the process plants running.
Right from planning and assembly to commissioning, the customer was able to lean back and relax – thanks to the competent support provided by Kremsmueller.
High-quality plastic is manufactured in the reactor. It is a decisive factor for the product quality that the tank must be free of traces of machining on the inside. Grinding and electro-polishing resulted in a glassy smooth surface with impressive precision. The requirements for optimum gas distribution were just as stringent. The production gas now reaches the reaction chamber through no less than 1228 guiding pipes.
The finished tank is 21 metres long, weighs 72.5 tonnes and has a diameter of 4.6 metres at its broadest point. The gigantic reactor was installed together with 180 tonnes of equipment, 170 tonnes of steel structure and 190 tonnes of piping. The entire I&C systems were also installed by the electrical engineering experts from Kremsmueller – using 86 kilometres of energy and instrument cables. Needless to say, the safety measures in the areas with explosive atmospheres were extremely stringent. The assembly work was so painstakingly planned in 3D that running operations were hardly disturbed: 90 percent of the work was carried out with the process plants running.
Right from planning and assembly to commissioning, the customer was able to lean back and relax – thanks to the competent support provided by Kremsmueller.
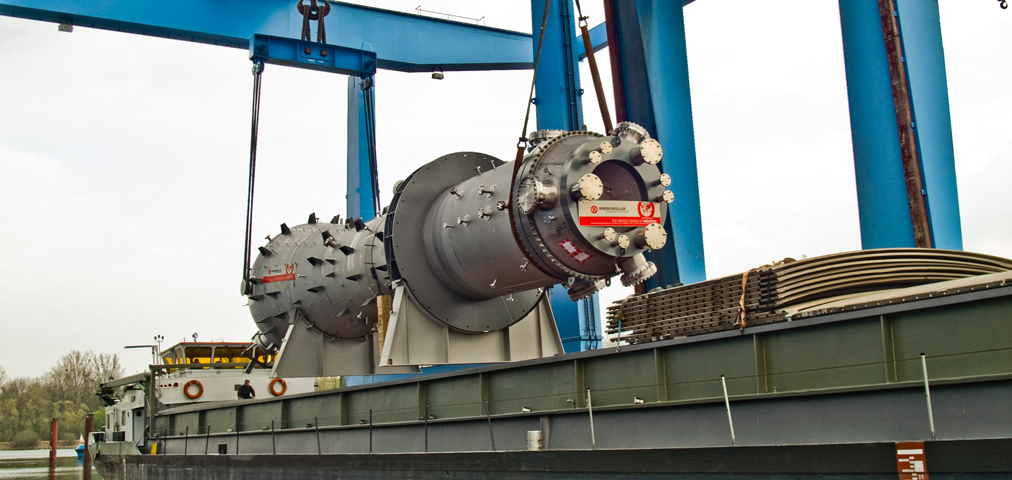
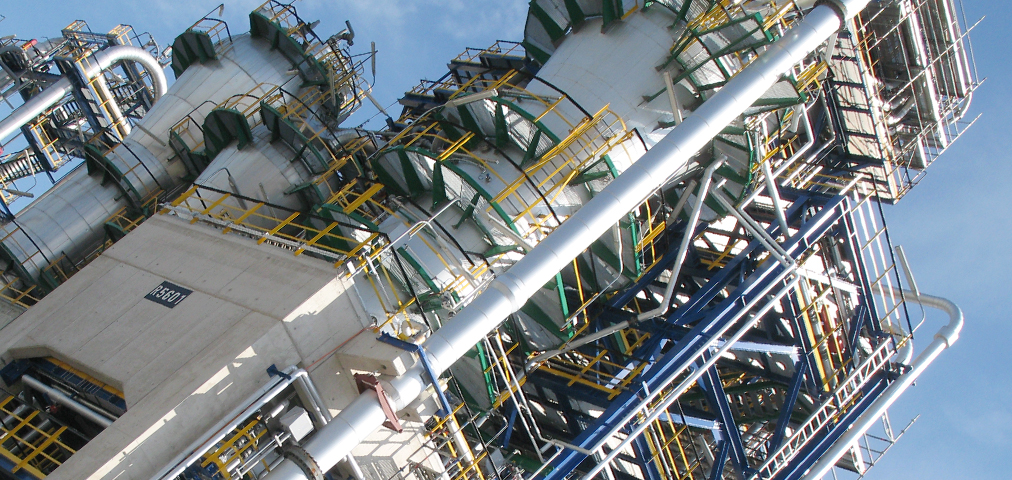
